The Advantages of Expert Packaging Equipment Service and Upkeep
The Advantages of Expert Packaging Equipment Service and Upkeep
Blog Article
Comprehensive Product Packaging Devices Solution to Ensure Peak Efficiency
In the world of packaging procedures, the relevance of extensive tools solution can not be overemphasized. By accepting a proactive upkeep method, organizations can reduce the dangers connected with unforeseen equipment failures.
Significance of Normal Upkeep
Routine upkeep of packaging equipment is crucial for guaranteeing optimal efficiency and durability. Such maintenance techniques not only prolong the life-span of the equipment yet also improve operational efficiency. By regularly checking and servicing equipment, businesses can recognize prospective issues before they rise right into pricey break downs, therefore lessening downtime.
Among the primary advantages of regular maintenance is improved product quality. Equipment that is well-kept runs even more accurately, guaranteeing regular product packaging stability and lowering the danger of defects. This is particularly important in industries where product packaging compliance is vital, such as food and pharmaceuticals.
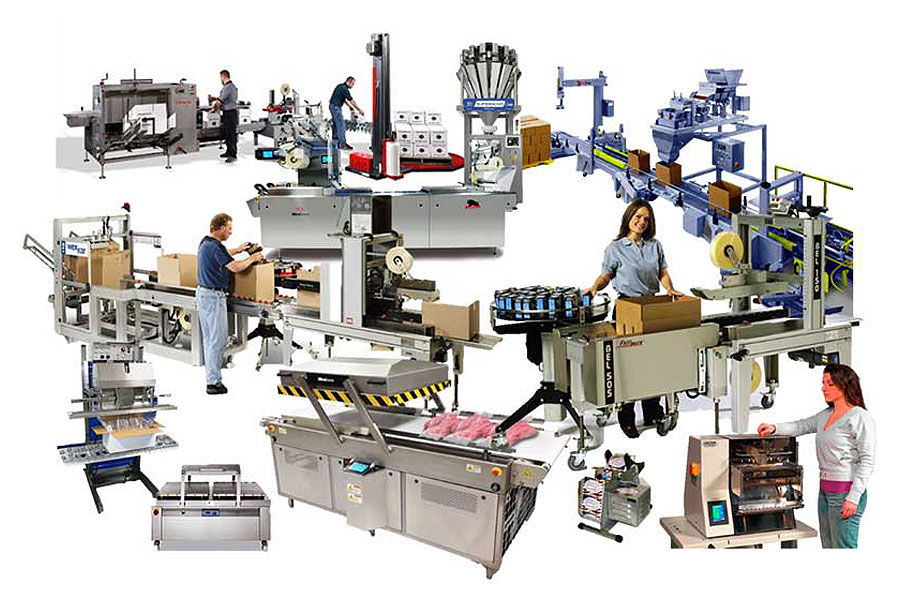
Trick Parts of Service
Reliable product packaging devices service includes numerous essential elements that are necessary for preserving peak functional performance - packaging equipment service. Routine examinations are essential. These evaluations recognize wear and tear, making certain that possible issues are resolved before they escalate into expensive breakdowns
One more vital part is calibration. Correctly adjusted devices warranties precision in packaging processes, which directly impacts product high quality and compliance with sector requirements. In addition, prompt replacement of used parts is important; utilizing OEM (Original Tools Manufacturer) parts aids maintain devices honesty and prolongs its life expectancy.
Educating employees is equally crucial. Well-trained operators are a lot more skilled at recognizing abnormalities and executing basic operating procedures, which improves general performance. Moreover, paperwork of service documents gives a historical summary of upkeep tasks, promoting better decision-making for future service needs.
Lastly, effective communication with service companies promotes a collective technique to devices administration, permitting tailored options based on operational demands. By integrating these essential parts, services can make sure that their packaging equipment stays reputable, effective, and qualified of meeting manufacturing needs, eventually contributing to an extra efficient manufacturing setting.
Proactive vs. Responsive Methods
Preserving product packaging devices can be come close to via 2 distinctive strategies: positive and responsive. By concentrating on avoidance, firms can improve the long life and integrity of their tools, minimizing the risk of unforeseen break downs that can disrupt procedures.
Conversely, a responsive strategy is characterized by reacting to problems just after they emerge. This technique normally entails resolving tools failures, which can lead to substantial downtime and costly repairs. While some companies might select this approach as a result of regarded cost savings, it typically leads to a cycle of persisting troubles and inadequacies. Relying solely on responsive upkeep can prevent a firm's capacity to enhance production schedules and fulfill consumer needs promptly.
Eventually, the selection between aggressive and reactive maintenance strategies can substantially influence the performance of packaging operations, impacting both operational performance and general profitability. Taking on a proactive way of thinking not only safeguards tools efficiency but additionally promotes a society of constant renovation within the company.
Benefits of Timely Upgrades
Carrying out prompt upgrades to packaging tools can considerably boost operational efficiency and product high quality. Frequently upgrading equipment ensures that organizations utilize the current technical advancements, which can improve operations and lower downtime. More recent equipment typically includes enhanced automation and accuracy, bring about faster production rates and reducing waste.
Additionally, timely upgrades can enhance compliance with market requirements and laws - packaging equipment service. As product packaging demands progress, out-of-date tools might not satisfy new why not check here safety and security or environmental guidelines, risking costly penalties and damaging a company's credibility. Upgrading devices not just minimizes these threats however additionally placements business as sector leaders devoted to top quality and sustainability
Furthermore, modern equipment commonly incorporates sophisticated monitoring systems that provide real-time data. This data can be very useful for making notified choices regarding upkeep, manufacturing scheduling, and inventory administration, inevitably driving productivity.
Finally, timely upgrades can enhance staff member satisfaction. Devices that runs successfully and reliably lowers frustration for employees, cultivating an extra productive job atmosphere. Finally, prioritizing routine upgrades to packaging devices is vital for preserving a competitive side and ensuring long-term success in the market.
Choosing the Right Service Service Provider
Picking the appropriate solution provider for packaging devices maintenance and upgrades is vital for browse around this web-site making the most of the benefits of timely improvements. An appropriate companion not just guarantees that your equipment runs successfully yet additionally expands its life expectancy, ultimately adding to your organization's profits.
When picking a company, consider their sector experience and know-how. Try to find business with a tried and tested track record in servicing the certain kinds of devices you utilize, as knowledge with your modern technology can result in more efficient options. Furthermore, examine their response time and accessibility; a provider that provides prompt assistance can mitigate downtime and keep your operations running smoothly.
Lastly, gather responses from other customers to determine satisfaction degrees and the service provider's online reputation. By extensively vetting possible solution partners, you can guarantee that you are making an educated choice that straightens with your operational goals.
Verdict
In final thought, thorough packaging tools solution plays a vital role in keeping machinery performance and long life. In addition, picking a competent service copyright makes sure that equipment is serviced with OEM components, leading to improved item quality and staff member satisfaction.
Report this page